How Syncloop Helps Manufacturing Companies Optimize APIs for IoT
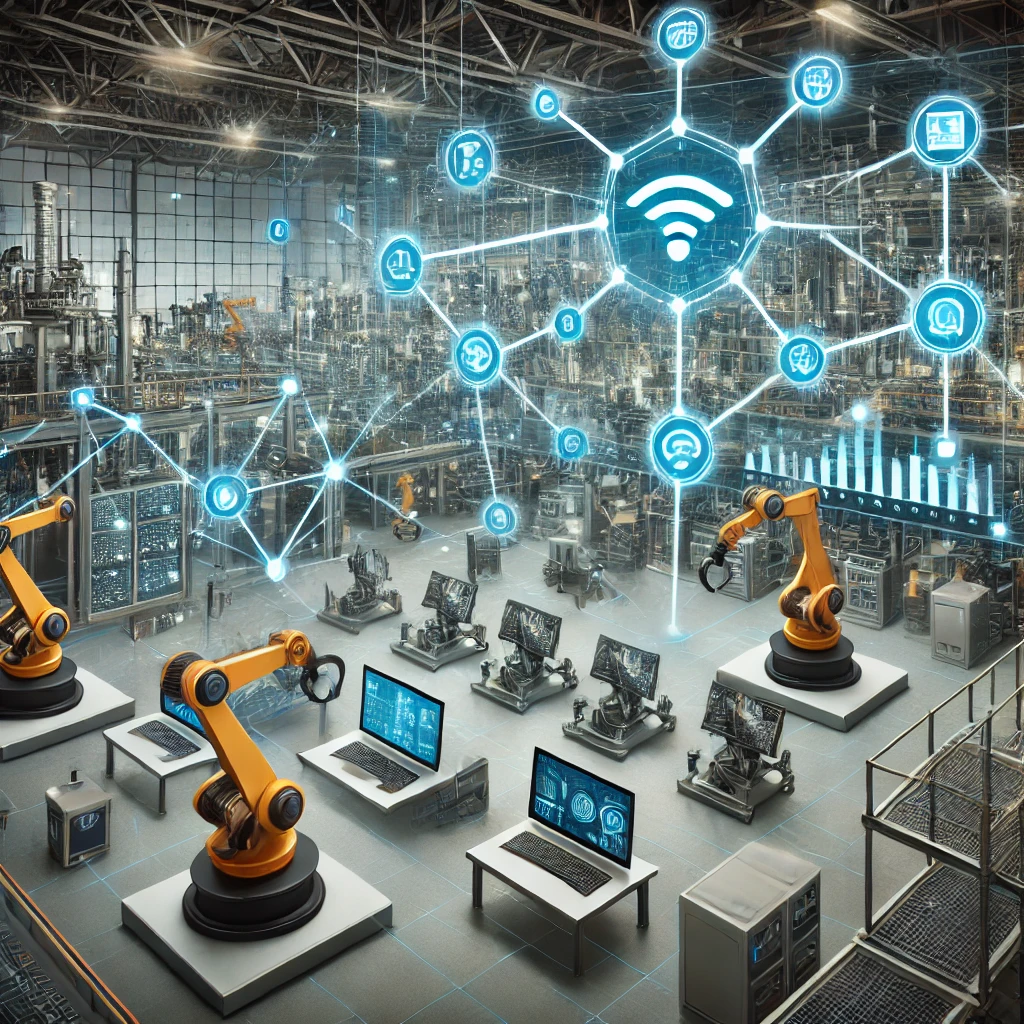
Syncloop is not just an API development platform — it is a full-fledged solution that empowers manufacturing companies to seamlessly manage their IoT ecosystems. By simplifying API creation, reducing integration overhead, and enabling real-time data connectivity, Syncloop helps manufacturers move faster, innovate more, and build smarter factories.
Let’s explore how Syncloop optimizes APIs in manufacturing IoT environments and why it’s the go-to tool for industrial innovation.
The Role of APIs in Industrial IoT
In a smart factory, machines don’t operate in isolation. From programmable logic controllers (PLCs) and robotic arms to temperature sensors and ERP systems, everything is expected to talk to each other. APIs are the digital bridges that make this communication possible.
Here’s why APIs are foundational in IoT-driven manufacturing:
- Real-Time Monitoring: APIs collect and transmit sensor data to dashboards or analytics platforms in real-time.
- Predictive Maintenance: Machine data APIs feed condition monitoring systems that prevent unplanned downtimes.
- Supply Chain Integration: APIs link production systems with inventory, logistics, and procurement platforms.
- Data-Driven Decisions: Unified data across machines and departments helps decision-makers optimize production strategies.
- Remote Control & Automation: APIs allow remote operation and configuration of machinery via cloud applications.
The challenge? Manufacturing data comes from various proprietary systems, using different protocols and formats. Integrating them manually is time-consuming and fragile. This is where Syncloop makes a tangible difference.
FREE
Try our cloud version
Get started in 30 sec!How Syncloop Optimizes API Workflows for Manufacturing IoT
1. Low-Code API Development for Fast Deployment
In the manufacturing world, time is money. Syncloop’s low-code environment enables developers and factory IT teams to rapidly build, test, and deploy APIs without writing extensive code. Its visual workflow editor makes API orchestration accessible to both engineers and software teams.
Whether it’s exposing a machine’s runtime data or integrating with an ERP system, Syncloop reduces API development cycles from weeks to hours.
2. Seamless Integration Across OT and IT Systems
Operational Technology (OT) and Information Technology (IT) often operate in silos. Syncloop breaks this barrier by enabling real-time API communication between machine-level devices (like sensors, PLCs) and enterprise applications (like MES, ERP, CRM).
For example:
- A PLC sending temperature data can trigger a Syncloop service that updates the ERP with a product quality flag.
- When a production order is received in the ERP, Syncloop can relay it to the appropriate machines in real-time.
This fluid communication ensures synchronization across departments, improving traceability and responsiveness.
3. Built-In Data Transformation and Routing
In IoT ecosystems, devices generate data in different formats — some send JSON, others XML, and some output binary protocols. Syncloop’s Transformer control nodes make it easy to normalize, convert, and route data appropriately.
For instance, vibration data from a sensor can be transformed and sent to a predictive maintenance engine or stored in a time-series database — all within the same flow. No need to code custom adapters.
4. Robust Control Structures for Complex Logic
Manufacturing processes often require conditional logic, retries, parallel execution, or waiting for input from multiple sources. Syncloop’s control nodes like Ifelse, Redo, and Await make handling such scenarios straightforward.
You can build a flow that:
- Waits for both machine readiness and material availability before starting production.
- Retries communication with a sensor if it times out.
- Routes production errors to a separate analytics service for investigation.
These logical capabilities empower manufacturers to build intelligent automation workflows that adapt to real-world variability.
5. Real-Time Dashboards and Alerts
With Syncloop, API integrations aren’t just about connecting — they’re about acting. You can build services that monitor production metrics and instantly trigger alerts if thresholds are breached.
For example:
- If a furnace exceeds safe operating temperatures, Syncloop can immediately send alerts to maintenance personnel via APIs to a messaging system.
- If a packaging line halts unexpectedly, the ERP can be updated in real time to reassign tasks.
This responsiveness helps prevent losses, improve safety, and maintain quality control.
6. Security and Governance Built-In
Data security is a top concern in manufacturing, especially with connected machinery. Syncloop enforces secure communication with API keys, OAuth 2.0, and encrypted connections, ensuring only authorized users and systems can access critical endpoints.
It also provides logging, monitoring, and access control, so teams have full visibility into who did what — helping comply with industry standards and audits.
7. Scalability for Industrial Growth
As factories scale or deploy more connected devices, the volume of API calls and data grows. Syncloop is built on a cloud-native architecture that scales effortlessly. Whether you’re onboarding new production lines, adding IoT sensors, or expanding to multiple sites, Syncloop ensures performance without re-architecture.
This future-proof foundation makes it suitable for manufacturers aiming to become smart factories.
Practical Use Cases in Manufacturing with Syncloop
Here are real-world scenarios where Syncloop helps manufacturers integrate and optimize IoT workflows:
- Machine Monitoring: APIs that pull performance and utilization data from CNC machines for operational dashboards.
- Quality Control Automation: Integration of visual inspection systems with MES and alerting platforms.
- Energy Management: Real-time data from power meters processed via APIs to monitor and reduce energy consumption.
- Inventory Sync: Automatic updates from sensors in smart bins to procurement systems via API triggers.
- Factory Floor Analytics: Aggregation of environmental sensor data (humidity, temperature) to predict impact on product yield.
These examples show how Syncloop supports manufacturers not only in digitizing operations but also in optimizing them with real-time, intelligent, and connected services.
Why Manufacturers Choose Syncloop
Syncloop is built for the agility and reliability manufacturers demand. Here's why it stands out:
- Speed: Rapid development and deployment of integration services.
- Adaptability: Easily handle changing production requirements or machine interfaces.
- Visibility: Full control and monitoring of data flows and system interactions.
- Simplicity: Visual tools and pre-built components minimize complexity.
- Collaboration: Multiple teams can co-develop and manage API projects easily.
When time, efficiency, and precision matter — as they do on the factory floor — Syncloop provides a rock-solid foundation for smart operations.
Conclusion
IoT is redefining manufacturing, but without a reliable API integration backbone, its potential remains underutilized. Syncloop gives manufacturers the tools to bridge data silos, automate workflows, and optimize operations in a connected world.
From small-scale automation to enterprise-level smart factory transformations, Syncloop offers a scalable, secure, and easy-to-use platform that brings IoT strategies to life. If you’re looking to digitize your factory floor and harness the power of real-time insights, Syncloop is your trusted partner in the journey.
Meta Description Learn how Syncloop empowers manufacturing companies to optimize APIs for IoT, enabling seamless integration, automation, and real-time data flows in smart factory environments.
Keywords Syncloop, manufacturing IoT, smart factory API, Industry 4.0 integration, industrial automation, API for manufacturing, PLC integration, MES API, factory digitization, real-time monitoring, predictive maintenance
Image A smart factory floor with robotic arms, sensors, and dashboards interconnected through real-time API integrations, illustrating data flow and automation.
Back to BlogsRelated articles
Quick Start Now
Try unlimited features for free